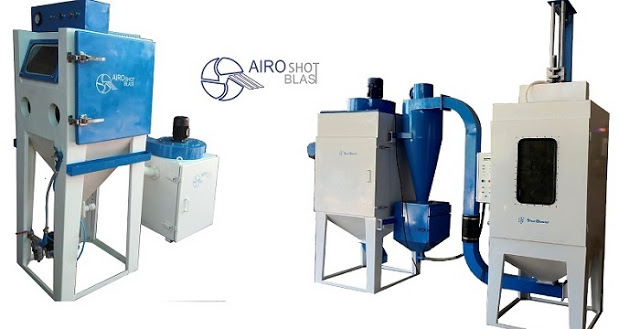
The shot blasting machine makes use of a mechanical method of propelling abrasive media using a centrifugal wheel to remove a layer of the surface and impurities from the surface of metal and steel products. There are three basic purposes that require the need to blast before finishing the product:
- It cleans and descales the surfaces
- Enhances paint adhesion by adding texture to the surface of metal products
- Efficiently reduces maintenance costs by increasing the life of the coating
This machine is used to remove unwanted corrosion and metallic waste on the surface of finished goods. This is done for making the surface uniform and to make it smoother for a better finish after paint or other applications. The process also works for cleaning rust, the roughness of the surface and further fabrication. It is used for cleaning the rough edges of different parts of an automobile or any other moulding parts that have sharp surfaces and uneven.
One of the most commonly used abrasive media for this blasting procedure is sand, this is the reason this process is most commonly referred to as sandblasting. Other than sand, there are numerous other materials that are also used for blasting. Some of these materials are glass beads, garnet, olivine, and chilled iron. Garnet and chilled iron materials are extremely coarse and abrasive in nature and therefore cannot be used for blasting on soft materials. Glass beads and olivine are most commonly used for the purpose of polishing the surfaces. These can be conveniently used for elements like rubber, glass, metal, and plastic.
Types of Shot Blasting Machine
The blasting process involves the use of two technologies:
- Wheel Blasting (Air Less Shot Blasting) Technique
- Air Blasting ( Pneumatic Shot Blasting / Air Operated Shot Blasting)
As part of this technique of blasting, a controlled stream of abrasive shot material is propelled towards the metallic or steel surface that needs to be shot blasted with. There is a blast wheel that is located at the heart of the machine. As soon as the rotation of the wheel starts, the metallic abrasives or the shot media are channelized towards its center. From this position onwards, the abrasive media are accelerated and hurled into the direction of the surface which is being prepared for finishing. After the completion of this process, the contaminants, as well as the media, make a rebound into a separation system that contains the dust collection system. Just like the name suggests, the dust collector is responsible for collecting or for removing the media that is pulverized, contaminants or dust. The remaining media gets recycled by returning it to the storage hopper where the particles can be kept for using them in the future.
Related Post:-