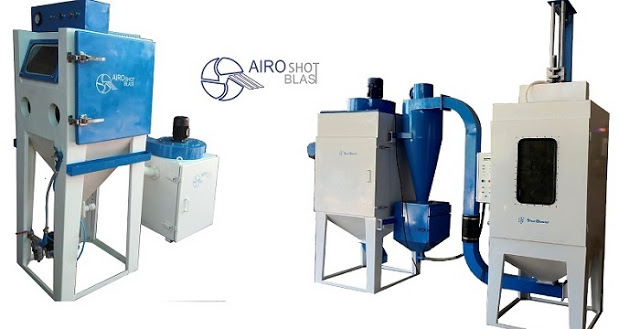
WHAT IS SANDBLASTING?
Regardless of the abrasive media, the term “sandblasting” refers to the method of moving that abrasive media with compressed air. This cleaning and preparation method takes compressed air as a power reference and directs a high-pressure stream of abrasive media toward the given surface. That surface can be auto parts being washed of dirt, grease, and oil. It could be rusty chains in a shipyard being reconditioned. Or the surface could be old filing cabinets being prepped for powder coating.
Sandblasting is a proven pre-finishing technique that’s been around for over a hundred years. Sandblasting equipment has developed from uncontained, free-spraying streams of sand creating noxious dust clouds to highly sophisticated contained enclosures with precise abrasive stream control. Sandblasting’s media also changed from sand to more user-friendly materials.
WHAT IS SHOT BLASTING?
The term “shot blasting” refers to the method of explosive abrasive media material with centrifugal or mechanical force. Shotblasting has a completely different compressed system than sandblasting. This abrasive treatment system uses a device similar to a spinning wheel to centrifugally accelerate shot-like material and blast it against a surface.
Shotblasting is a much more rampant abrasive technique than sandblasting. It’s usually used for larger and more difficult preparation objects that need a strong application force and a denser media material to clean and prepare a surface. Shotblasting also requires strict containment as the force of blasted shot could cause warrant damage if the process isn’t confined.
Equipment used in sandblasting
Sandblasting uses high-pressure compressed air to move blasting media on the project. This reliable technique suits a wide range of surfaces and a variety of treatments including a variety of abrasive media. Sandblasting equipment contaminants such as excluding rust, grease and old paint to give surface adhesion for new coatings. Sandblasting systems include these components:
- Airblast rooms: These are clean rooms that are environmentally controlled with abrasion media recovery for highly-productive and efficient operations.
- Airblast tumble equipment: This equipment consists of mill driven tumble blast machines that use oscillating nozzles and cyclone separators inside a rubber-lined chamber.
- Portable blasting stations: Mobile air blast methods have pressure pots in various sizes for increased productivity in portable configurations.
- Blast cabinets, suction, and pressure: This stationary sandblasting equipment also ranges in size. It uses a siphon feed system and a balancing pressure regulator to ensure equilibrium inside the blast cabinet.
- Bulk blasting systems: These are large sandblasting systems available in stationary models or truck-mounted for total portability.
- Blast and recovery systems: More advanced sandblasting equipment have systems that blast and vacuum simultaneously and avoid any open-air contamination.
- Cryogenic deflashing systems: Very cold temperatures allow certain surfaces like rubber, diecast, plastic, magnesium, and zinc to be deflated with precision.
- Wet blast equipment: Occasionally, sandblasting equipment uses water to eliminate friction heat and prepare surfaces by scrubbing instead of abrasion caused by dry blasting.
Equipment used in shot blasting
Shot blasting uses wheel blast equipment to establish abrasive media on surfaces being treated for final finishing. This equipment uses a specifically produced and closely checked wheel to generate efferent force and blast abrasives like steel shot and steel grit on products. The process includes “throwing” media at a surface preferably than “blowing” it. This is the general equipment used in shot blasting systems:
- Tumble blast equipment: Tumble blast equipment allow continuous blasting cycles with continual abrasive recycling. These types of machines have built-in rubber belts and steel flight models.
- Swing table blast wheels: Direct drive blast wheels swing out for loading and unloading abrasive media.
- Table blasters: These are fixed equipment components with direct drive wheels connected inside the blast cabinet.
- Spinner hangers: These personal drive blast wheels have turning spindles that allow loading and unloading abrasive media.
- Hanger blast equipment: Blast systems can be fitted with trolleys and hung on manual Y-track monorails for specific shot blasting operations.
- Cylinder blasters: Special shot blast equipment concentrates on eliminating rust and old paint from all forms of metal cylinders.
1 thought on “What is the difference between shot blasting and sandblasting?”